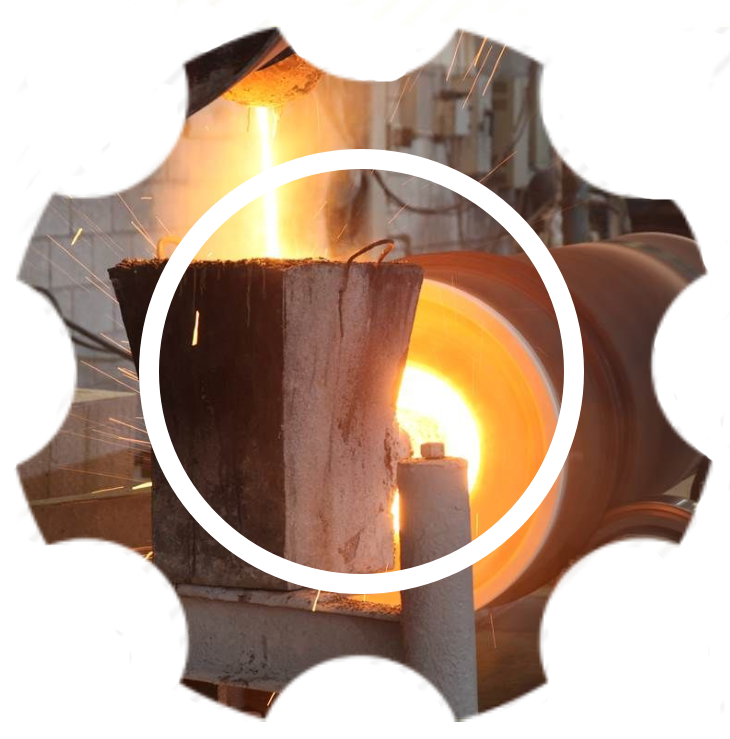
Centrifugal Castings At Cast Alloy Products LLC,
• Centrifugally tubes are made by spun casting. The advantage of the centrifugally cast tubes is the high purity of the Cr and Ni containing alloys. A certain amount of molten steel is filled into rotating molds.
• The high centrifugal forces press the liquid metal to the surface of the mold, and thus the tube shape is made.
• Due to the lower density of the impurities, they are concentrated in the inner side of the tubes and can be removed by pull-boring afterwards if required.
• Furthermore, by centrifugal casting the carbon content (0.4-0.5%) can be maintained higher as compared to drawn tubes (up to 0.1%)
Advantages of the Centrifugal Casting Process
There are a number of advantages to using centrifugal casting for the manufacture of cylindrical and circular parts, such as:
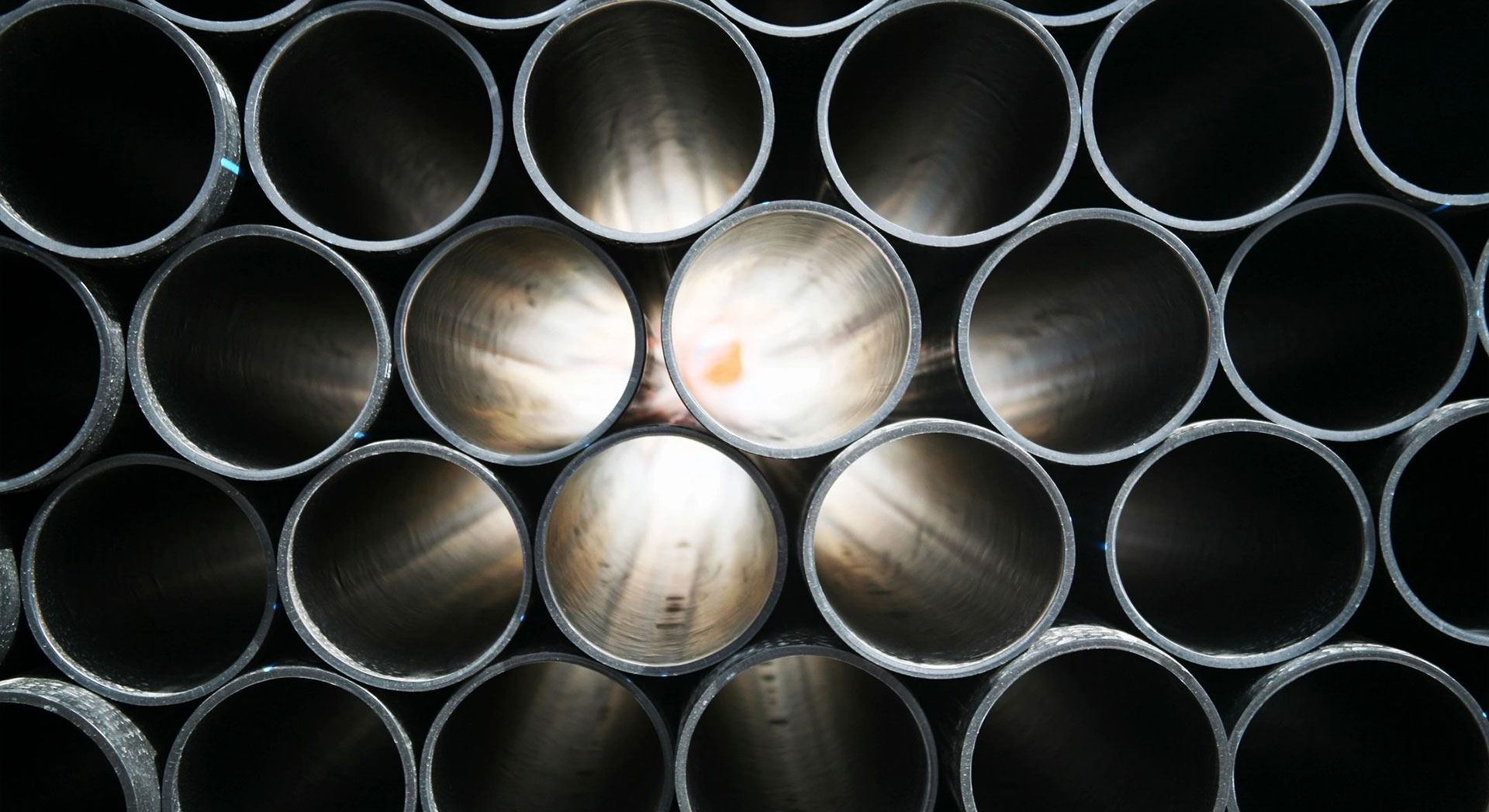